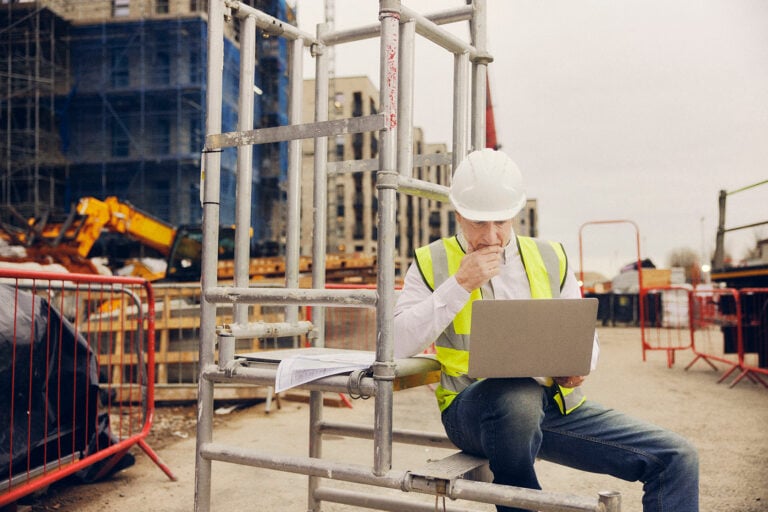
How the right tech can help you manage outgoing cash
Every 30 minutes a new company chooses our industry leading construction accounting technology to create greater operational efficiencies.
Sage financial products give you complete visibility into, and control of, all of project financials. Easily stay on top of job and labor costs, change orders, accounts receivables and payables, as well as purchase orders, work orders, and invoices. Customizable alerts warn when compliance issues or insurance issues arise. Automated payroll functionality manages multiple unions, pay scales, along with state and federal requirements.
Visit our website to learn more: https://www.sage.com/en-us/sage-construction/